What is a hydraulic cylinder?
The main driver of our business is hydraulic cylinders.
A hydraulic cylinder, also called a linear hydraulic motor, is defined as a mechanical actuator used to deliver a force through a linear stroke.
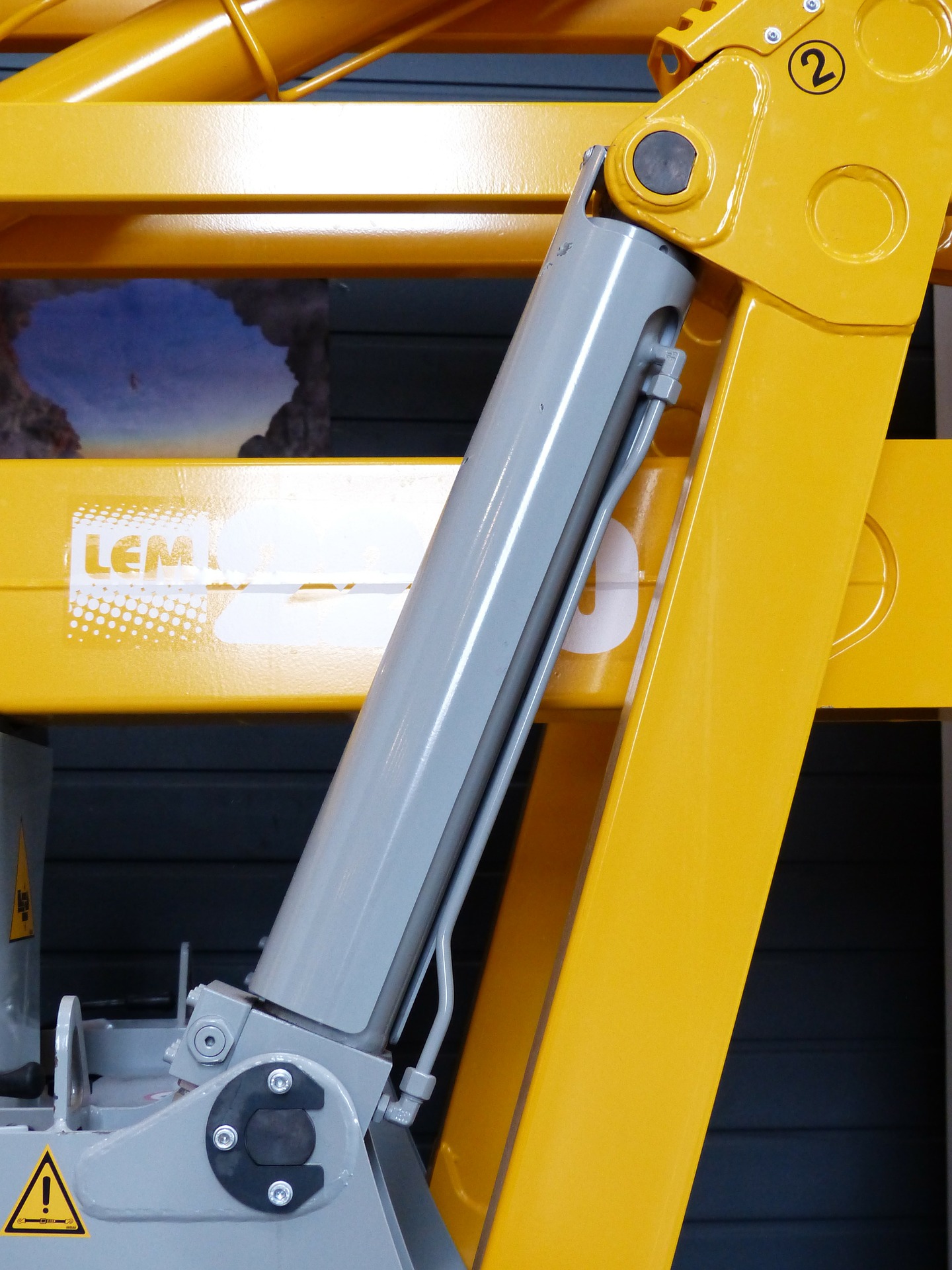
Hydraulic cylinders draw power from a pressurised hydraulic fluid, which is typically some type of oil. The hydraulic cylinder basically consists of two parts: a barrel cylinder and a movable piston or plunger connected to a piston rod. The barrel cylinder is closed at both ends, with the bottom at one end and the head at the other end, through which the piston is inserted and which has a bore through which the piston rod exits. The piston divides the inside of the cylinder into two chambers: the lower chamber and the piston rod chamber. Hydraulic pressure acts on the piston to produce the linear movement.
The maximum force is a function of the active surface area of the piston and the maximum allowable pressure, where: F = P * A
This force is constant from the beginning to the end of the stroke. The speed depends on the fluid flow and the piston surface. Depending on the version, the cylinder can apply tensile and/or compressive forces.
Generally speaking, cylinders can be classified into two groups: single-acting and double-acting.
The distinguishing features of the operation of both types are as follows:
- The force generation is only in one shaft direction in the case of the single-acting cylinder, while it is in both shaft directions in the case of the double-acting cylinder.
- Forward: in effective direction with hydraulic pressure vs. in both directions with hydraulic pressure
- Retract: with spring or external force versus in effective direction with hydraulic pressure.
- The restoring force is small in the first type (in general cases only minimal spring forces) and high in the second type.
- Spring chamber: in single-acting cylinders, the spring chamber must be ventilated because of the danger of water formation due to condensation and penetration of corrosive liquids, whereas this is not necessary in double-acting cylinders.
- The displacement times are not exactly definable in the former because of the spring recoil, and are strongly dependent on the tube cross-section and the viscosity of the oil. In the latter, however, the times are exactly definable and repeatable.
- In terms of operational safety, single-acting cylinders may fail due to spring breakage, whereas double-acting cylinders have a high operational safety.
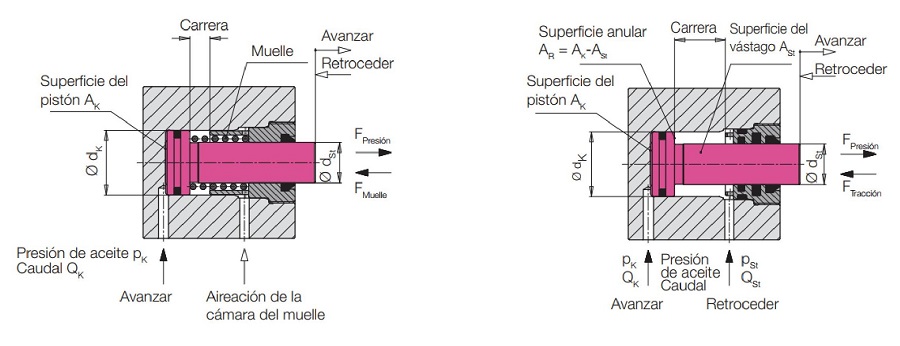
Single-acting hydraulic cylinder initial position Double-acting hydraulic cylinder initial position
Leave A Comment
You must be logged in to post a comment.